Combustion Chamber of Turbo Engines
What is Tungsten Alloy Turbo Engines?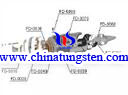
As we know,tungsten alloy turbo engine is the heat engine which is conditioned by their maximum intake temperature, and tungsten alloy turbo engine is limited by the behavior of the constituent materials of the articles that are most exposed to heat and constraints. Tungsten alloy turbo engine is widely used in aviation.
Why Choose Tungsten Alloy Turbo Engine?
Concerns for environmental protection have led designers of aviation tungsten alloy turbo engines to search for means to reduce the proportion of pollutants in the exhaust gases of the engines. It is known that the principal problems in the matter of pollution of aviation tungsten alloy turbo engine is the emission of carbon monoxide, of hydrocarbons, and of various unburnt residues during operation on the ground and, on the other hand, the emission of nitrogen oxides and of particles during take-off and during cruising at altitude. Therefore, tungsten alloy turbo engines are increasingly accepted by public in this case.
Conventional combustion chambers are generally of optimized rating for take-off or near take-off operation. This signifies that, in the primary zone of the combustion chamber, a fraction of the air flow of the compressor is introduced so that, with the injected fuel, the fuel-air mixture in this zone would be essentially stoichiometric in these modes. Under these conditions, due to the levels of temperature and high pressures, as complete as possible a combustion is obtained, combustion yields greater than 0.99 are attained, the speeds of the chemical reaction being optimum for these stoichimoetric mixtures.
In contrast, at low ratings, at idle or nearly so, the total richness in the combustion chamber is only about half that at take-off; in addition, the pressures and temperatures at the outlet of the compressor are lower; the result is that the combustion chamber, with the partial charge is very much maladjusted and that the slow speed combustion chambers efficiency rarely goes beyond 0.93. The combustion chambers is, therefore, very incomplete, which means much higher concentrations of carbon monoxide and unburnt residues at the exhaust than under normal operation. The proportions of the pollutants are all the higher, the lower the total yield of the combustion chambers.
However, it appears to be possible to improve the performance of a combustion chamber by acting on four factors:
The timing of vaporization of the fuel,
The timing of the air-fuel mixture,
The timing of the fresh gas/burnt gas mixture,
The timing of the chemical reaction.
The first two times can be considered negligible at high ratings because of the pressures which are attained, but it is not so at low ratings. In fact, in order to increase the speed of the vaporization of the fuel, it must be transformed into fine droplets, which is easily realized by the conventional mechanical atomizing injector, but the performance which is obtained in the lower ratings is poor. This is due to the fact that, if the fuel is well divided into droplets, these are poorly mixed with air in the primary zone and local zones would appear which have a richness which is too high. In the end, it would be necessary that each droplet would have around it the quantity of gas necessary for its vaporization and for its combustion in combustion chambers, i.e., a quantity of gas which results in a stoichiometric mixture with the oxygen molecules after complete varporization. In order to accomplish this, systems such as aerodynamic injection have been proposed. Aerodynamic type injectors generally comprise whirling, or swirler vanes through which the air from the compressor is introduced, which serves to atomize the fuel. An air/fuel pre-mixture is thus obtained.
The fresh gas/burnt gas mixture must also be advantageous because tungsten alloy turbo engine contributes to the increase in the temperature of the carburized mixture and, therefore, aids in its atomization and consequently permits an improvement in the speed of the chemical reaction. In conventionally allowing this contact of the carburized mixture with the high temperature gas from the combustion chambers it is desirable to arrange for a recirculation of the latter by searching for a convenient turbulence level.
All of these solutions, which allow an improvement in the combustion chambers yield have, however, a maximum efficiency only for values sufficient for the pressures and temperatures of the air at the combustion chamber inlet.
As far as the reaction time is concerned, it is necessary to additionally research an optimization of the richness of the mixture, the ideal would be to be able to obtain a stoichiometric air/fuel proportion in the flame stabilization zone, regardless of the operation of the engine.
A first objective of this product is to provide a novel solution to the problem of low operating combustion chamber which includes aerodynamic type or pre-atomization injectors, which are mounted in the base of the chamber. In fact, in the case of a conventional combustion chamber of this type, which is arranged to provide a stoichiometric mixture at take-off, about one-third of the air flow necessary for the combustion chamber is introduced in the injection system and two-thirds by the primary orifices.
All of these factors are advantageous for a reduction of the reaction times and could lead to a reduction of the length of the combustion chamber and thus to a limitation of the dwell time of the gases in the tungsten alloy turbo engine.
As far as the combustion chambers of the annular or nozzle-shaped type are concerned, it is possible to design the intermediate segment in the form of an annular zone which is common to all the injectors. The intermediate segment would then be formed of a circular base located in a plane which is perpendicular to the axis of the combustion chamber to which the injectors are attached, and of two annular lateral walls which are welded, at the one end, to the circular base and on the other end to the base of the chamber, defining an annular volume which flares towards downstream, various forms could be adapted for the lateral walls, in a manner analogous to the case of the intermediate segment itself to each injector. Tungsten alloy turbo engines could each particularly be generated by a straight line and then each form a conic wall at the downstream end on which the holes, which are designed for the introduction of the fourth flow of air are located, distributed over one or several circles which are located on one or several planes which are perpendicular to the axis of the chamber. Each of the lateral walls could be formed of two truncated conical sections, with the connecting axes welded end to end, of which the angles at the top increase towards downstream, the small diameter holes which are designed for the injection of the fourth air flow being located immediately ahead of the joint which is formed by the joining of the two truncated cones, and distributed over one or several planes which are perpendicular to the common axis of the truncated cones. Combustion chambers could also be formed of a first truncated portion, with a top angle between 60° and 100°, comprising, at its downstream end, an annular zone which is located in a plane. Tungsten alloy turbo engine is perpendicular to the axis of the chamber, in which the small diameter holes are drilled, which are designed for the injection of the fourth air flow, the holes being distributed over one or several circles which are coaxial with the said zone and having their axis normal to the generators of the truncated portion, to which an annular zone is joined where they are drilled. This last arrangement proves to be particularly advantageous in the case of a high performance combustion chamber because of the fact that it suppresses the hot slip-streams behind the jets which correspond to the fourth flow.
The diameter of the holes, which are designed for the injection of the fourth flow, in the intermediate annular segment, which will represent 1/6 to 1/3 of the primary air, will have a diameter between 1/10 and 1/40 of the maximum dimension of the flared segment, measured on a radius of the chamber.
The cooling of the downstream ends of each lateral wall by a fifth air flow obviously works, the holes which are designed for the injection of this fifth flow being located in the immediate proximity of the joint between each lateral wall and the chamber, the values of the angles and the flow being identical to that mentioned in the case of the chambers for which each injector possesses its own intermediate segment.
The penetration of the intermediate segment could also be realized in order to increase the volume of the secondary recirculation zone; its depth of penetration will then be between one-fifth and one-half of the maximum dimensions of the intermediate segment, measured on a radius of the chamber.
Chinatungsten can offer tungsten alloy turbo engines used in this case not only according to international standard, but also as per customer’s requirements. Tungsten alloy is a suitable material for combustion chamber of turbo engines. So if you have any interest in tungsten alloy turbo engines, please feel free to email us: sales@chinatungsten.com, sales@xiamentungsten.com or call us by: 0086 592 512 9696, 0086 592 512 9595. We are at your service.